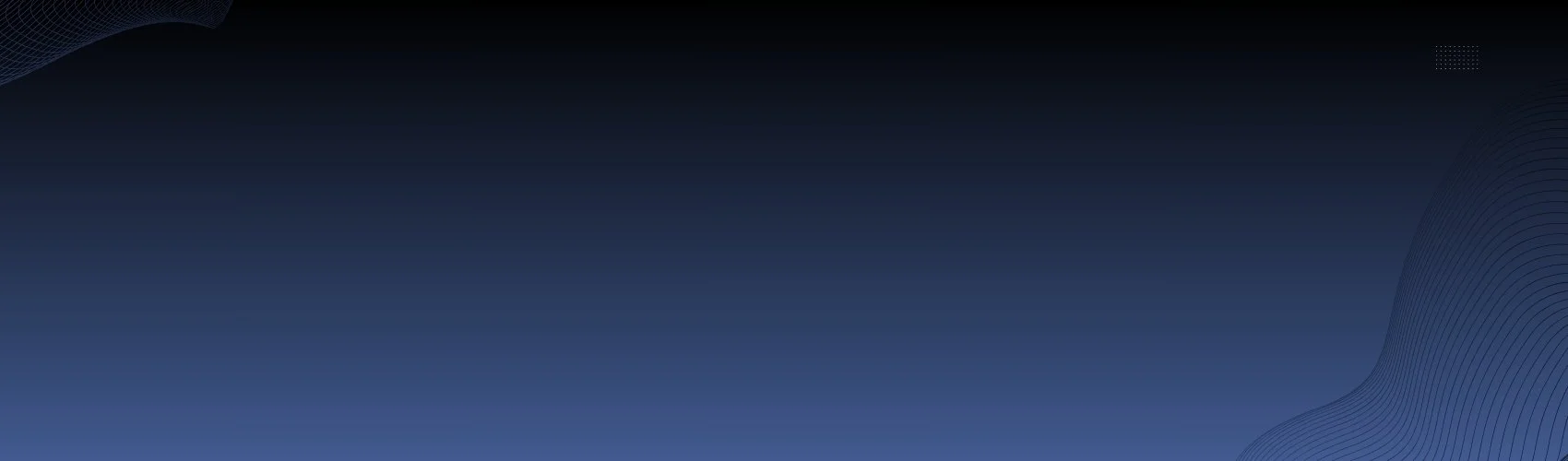
Blog Articles and Commentaries from Neil McCoy-Ward
Computer chip shortage strangling global manufacturing and killing economic recovery
The global chip crisis has arisen from a combination of events, creating a ‘perfect storm’ that is likely to cost the global economy billions of dollars.
Economics | Business | Finance | Employment | Tech | Real Estate | Environment